挑战
随着技术的进步,工程系统间交联越来越多,体系级系统更加普遍,体量更加庞杂,专业子系统的复杂度也呈指数级增加。传统的研制方式,在系统级设计还是以文档,画图为主,没有统一的系统级模型,缺乏有效的设计、分析和验证手段。
国际系统工程学会(INCOSE)提出“基于模型的系统工程”(MBSE)概念。定义MBSE为:“使用建模方法支持系统的需求定义、设计、分析、验证和确认等活动,这些活动从系统概念设计阶段开始,持续贯穿到系统开发以及整个产品生命周期阶段。”
在进行MBSE实践过程中,虽然在系统设计时引入了基于SysML的系统模型,解决了系统设计表达和逻辑验证问题,然而针对复杂工程系统的研发,会涉及到多专业学科,在机械、结构、电气、电子、液压、控制、软件等专业设计阶段已经积累的比较成熟的模型,面临如何在MBSE中应用的困扰。
在下文的案例中,重点展示如何实现以系统模型为核心,对不同专业学科模型的调度和联合仿真,解决跨工具、跨领域、跨尺度的集成仿真问题,推动MBSE的进一步落地应用。
MBSE应用案例
下文以“伺服液压系统”为例,展示MBSE在系统设计中的应用。该系统用于接收远程电子单元的控制指令,控制飞机方向舵的舵面偏转,由传感器、传动机构及一系列阀组成。在该案例中,针对伺服液压系统从问题域、方案域和实现域三个角度进行分析,实现了系统的需求分析、架构设计和仿真验证过程。
1)问题域
问题域定义的目的是用来分析和细化利益攸关者需要,通过SysML模型元素进行系统表达,针对系统要解决的问题得到一个清晰且一致的描述。
用例可以反映利益攸关者所重视的内容,并解决他们关切的问题。其中,伺服液压系统的主要应用场景为:在通电通压的情况下,接收REU的控制指令,实现对方向舵的控制,同时将系统运行状态实时反馈到飞控系统。因此,用例可划分为1个主用例(控制舵面)和2个子用例(控制偏转、检测状态)。
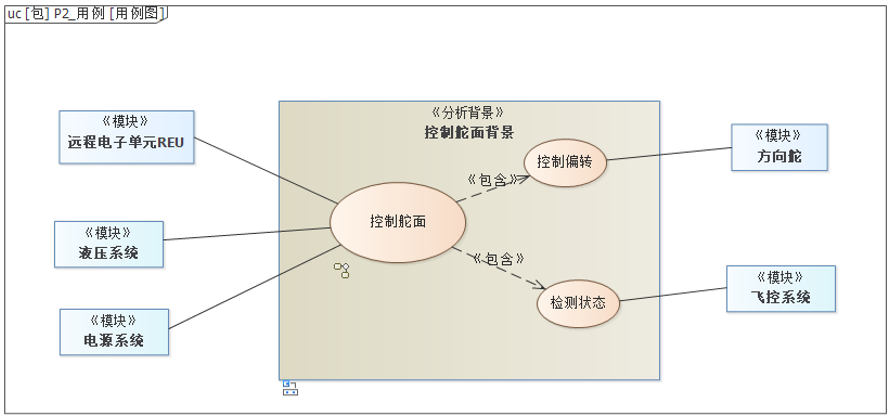
然后针对“控制舵面”用例,可通过带泳道的活动图对应用场景做进一步细化描述,可细化外部系统与伺服液压系统的具体接口信息和交互逻辑,梳理系统的运行分析过程,和明确系统所承担的具体功能。

2)方案域
此阶段的焦点定位于系统的解决方案,既包含系统功能、接口等的清晰描述,也包括在满足所有系统功能的基础上开发一个系统架构。
通过状态图可分析系统在其生命周期内的完整动态行为,包括定义系统的状态模型、激励模型(如外部信号,变更事件)、行为模型、UI模型。然后,执行状态机来检验所构建的模型是否符合利益攸关者期望,进而在产品研制的早期及时发现需求偏差与缺失。
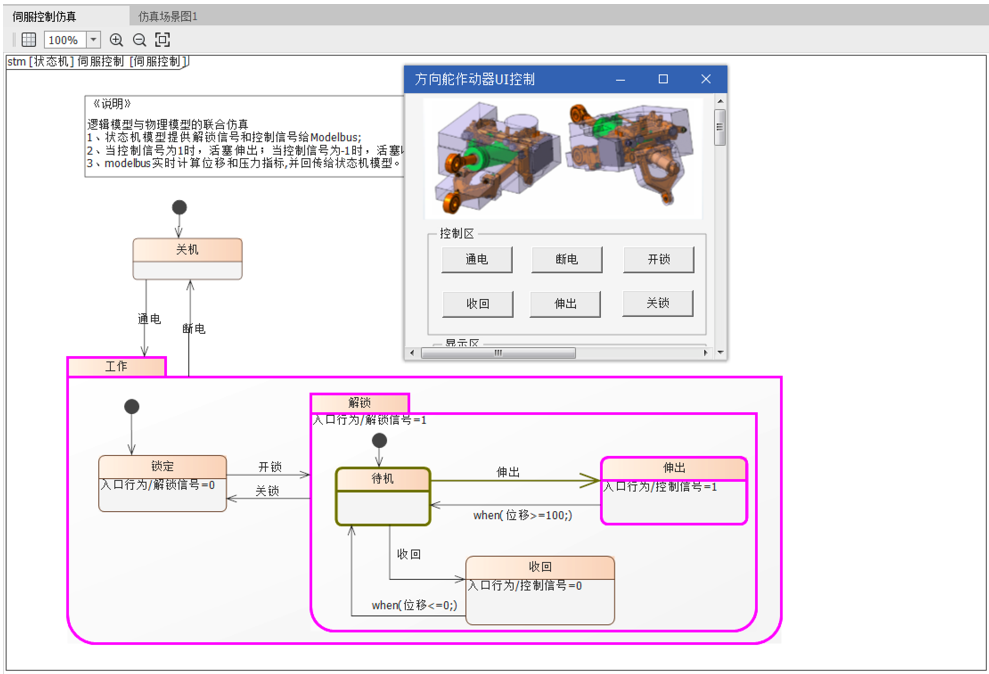
使用内部块图描述系统工作原理,将系统拆分成子系统,明确子系统间的接口。伺服液压系统物理层可被分解为电磁阀、电液伺服阀、模态选择阀、压力传感器等,根据指令类型,通过各种阀对进回油及油压的控制,实现活塞的伸出和收回,从而实现方向舵偏转。
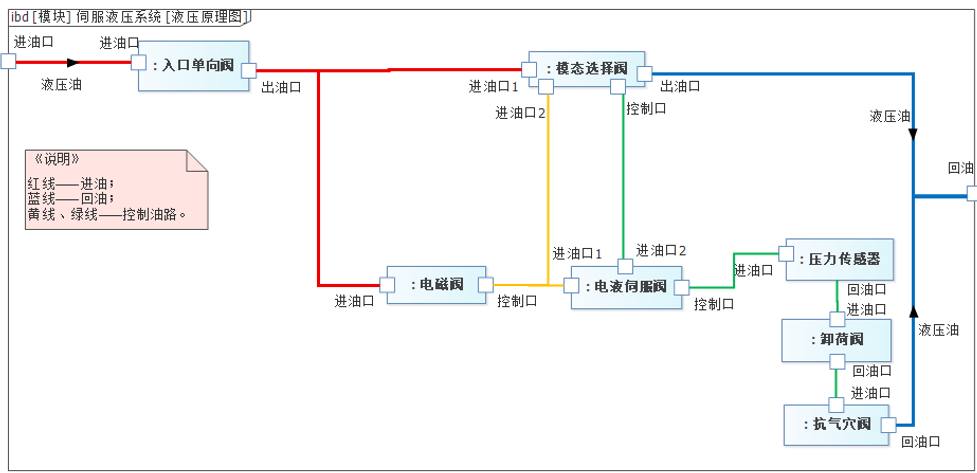
3)实现域
在民机飞控系统中,每架飞机方向舵舵面配备3台方向舵作动器,每台作动器配备一个REU伺服控制模块,3套伺服系统工作原理完全相同,以提供必须的系统余度,保证飞行可靠性和安全性。
该方向舵作动器具有两个工作模态:
主动模态:电液伺服阀接收REU控制输入电流指令分配负载流量,从而对作动筒的位置和速度来进行控制。主动模式要求电磁阀上电并要求液压系统压力高于一定的门限。
阻尼模态:在阻尼模态下,由于液压系统压力或REU指令信号的丧失,单线圈常闭电磁阀处于关闭状态,此时模态转换阀将处于阻尼工作位置。当模态转换阀处于阻尼工作位置时,模态转化阀将作动筒与伺服阀油液控制隔离。
根据方向舵作动器系统工作原理图,建立AMESim液压系统模型。
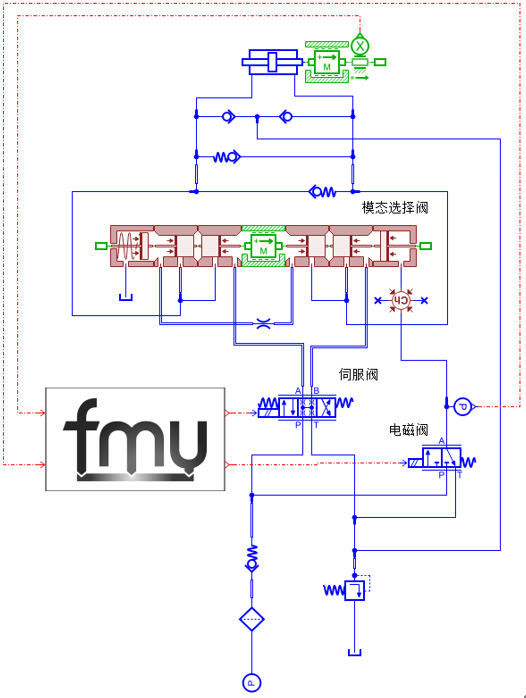
建立REU伺服控制模块的Simulink模型,描述作动器位置闭环控制的PID调节。

构建仿真场景,实现将逻辑模型与物理模型的联通。仿真场景图的作用体现如下:
Ø 导入伺服液压系统状态机模型;
Ø 导入通过modelbus绑定的多学科模型(AMESim液压系统模型和REU伺服控制模块Simulink模型);
Ø 导入用于展现人机交互的UI模型;
Ø 通过连线关联,实现逻辑模型与物理模型的参数绑定。
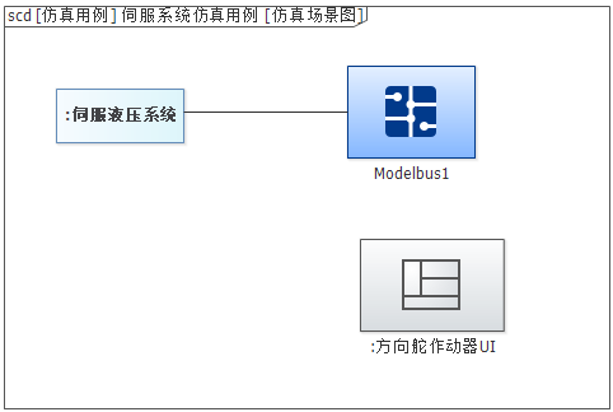
各模型之间的联合仿真接口数据交互关系主要为:状态机提供伺服指令和锁信号给模型总线,收到模型总线返回的活塞位移和液压压力指标。
在联合仿真过程中,首先通过UI模型提供外部激励给状态机模型(通电、开锁),实现系统状态跳转及信号发送。
同时,AMESim液压系统模型中的电磁阀接收状态机指令(对应解锁信号为0或1)控制模态选择阀换向,伺服阀控制方向舵作动器按REU给定的PID控制指令动作。在此过程中,液压系统模型上传到模型总线的数据为作动器位移和液压系统压力,从模型总线接收的数据为伺服阀的PID控制信号和电磁阀的锁信号。
状态机发出伸出、收回的指令信号(对应控制信号为0或1),由作动器输出的位移通过负反馈由PID控制作动器按指定位移100mm伸出、收回。在此过程中,Simulink控制系统模型上传到模型总线的数据为PID参数,从模型总线接收的参数为作动器位移和作动器伸出、收回的指令信号。
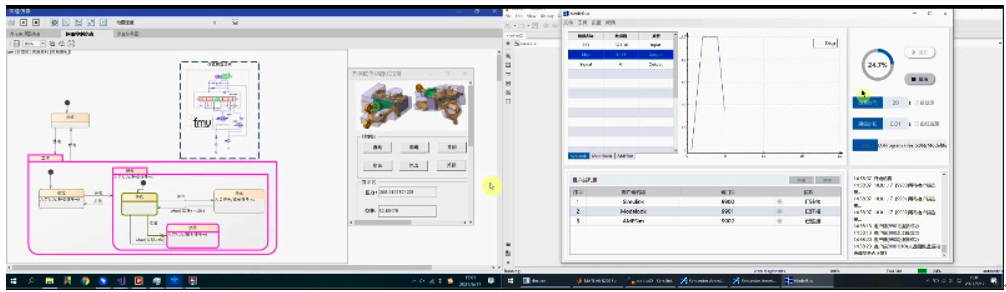
价值
通过问题域、方案域和实现域的逐层分析,形成了一套规范、可实施的设计方法;
在仿真时除了应用状态机中的离散信号外,引入了机、电、液、控、软等多学科模型,使仿真更贴近于实际;
实现了需求工程到仿真工程的局部贯通,数据贯通、工具贯通、业务贯通,促进MBSE进一步落地应用。
——END ——